Injection moulding is a forming process using moulds. Plastic Materials are heated and melted, and then pushed (Injected) into the mould where they are cooled to form the desired shape (that of the mould).
With injection moulding, parts with diverse geometries, including those with complex shapes, can be quickly and continuously manufactured in large volumes. Injection moulding is used to manufacture products in a wide range of industries and encompasses commodity items as well as precise engineering components.
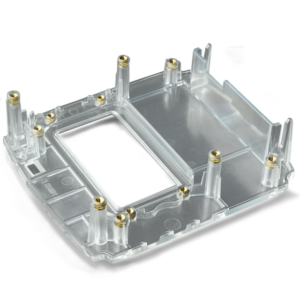
Injection Moulding Process
Typically, injection moulding begins with resin pellets (granules) that get poured into a hopper, the entry point for the material. The pellets are then heated and melted inside the cylinder in preparation for injecting them into the mould. The material is then forced through the nozzle of the injection unit before being delivered through a channel in the mould called a sprue, then through the runners/gate into the mould cavity. After the material cools and hardens, the mould opens, and the moulded part is ejected from the mould. The sprue and runner are trimmed from the part.
Injection Moulding Machine
The structure of an injection moulding machine consists of an injection unit that sends the melted materials into the mould and a clamping unit that operates the mould.
There are different types of injection moulding machines. That is, machines operated by servo motors, those operated by hydraulic motors, and hybrid machines that use both servo and a hydraulic motor.
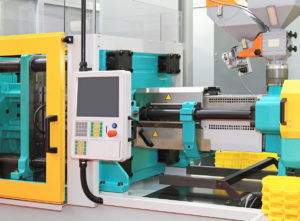
After an engineer designs a product, moulds are made by a mould-maker (or toolmaker) from metal, usually either steel or aluminium, through precision machining to form the features of the desired part.
Parts created for injection moulding must be designed carefully to facilitate the moulding process; the material used for the part, the part’s desired shape and features, the mould material, and the properties of the moulding machine must all be considered during the design phase. The versatility of injection moulding process is facilitated by this breadth of design considerations and possibilities.
Read more about Designing for Injection Moulding here.
If you’re looking for a partner in additive or traditional manufacturing, check out our capabilities today. We can help keep your projects moving forward – begin a quote now or contact an expert.