What is warping?
“Warping” occurs with many 3D printing processes, particularly when heating and cooling are involved, which cause material shrinkage, where the corners of the print lift and detach from the build plate. Stereolithography (SLA) and Selective Laser Sintering (SLS) can be affected most by warping; Digital Light Processing (DLP) can also be affected, but it’s not common because the build envelope is so small. Of these, SLS has the most potential for warping.
Our Quickparts team works to keep you aware of when a part can warp and what may cause it to do so. We watch for potential issues in everything from the design file to the temperature of our facility, the time of year, and when a piece will arrive at its destination and discuss any factors with you. These could include changing the shipping times, sending the part in a temperature-controlled shipping container, or adjusting your file.
Contributing Factors
Wondering what factors contribute to warping with your SLS or SLA print job? Here are a few things that can affect your final product.
Geometry
The project´s geometry, size, and design all play a role in whether a part warps. For example, thin, flat parts in general (like a box) can warp, but thicker areas can warp as well. Any flat area more than 152.4 mm is at risk of warping.
When we 3D print plastics, the materials first expand slightly and then contract as they cool. During the build process, the heat buildup in the printer can cause parts to warp. If the material contracts too much or too quickly, the print may bend up from the build plate. We work to control temperatures during the build to help with this aspect.
Sometimes, we can orient the part differently during the build, which can result in a better product, but this does not always work. In other instances, we can add braces to help, but we learned that braces on a boxy part can cause the part to twist and distort, which can be worse than warping.
Material
We can build SLS projects with a different material if we know the part will warp, and some materials carry a greater warp risk than others. If our customer needs a decently sized part to be flat, we typically advise them to build it with SLA because we know the part won´t be flat with SLS. Or we advise using a different material that we know will work better.
The primary concern for our customers is their intended use. Some SLS materials create strong parts and can be mounted repeatedly or put through some level of abuse. Other times, we recommend 3D printing the part in pieces and assembling them together, depending on the customer´s requirements and how they need to use it. The accuracy with respect to geometry can sometimes be better on a part produced in several assembled parts than on a monobloc part, which will present a greater risk of deformation. A show piece, for example, that will only be handled carefully will usually print well with SLA, but a part that must be mounted to an engine or endure hours of testing may function better with SLS.
Finishing
Even the finish chosen for a part can cause warping. If an SLA or SLS part requires paint, the paint can sometimes cause the piece to warp, especially if it is only on one side. This aspect isn´t affected by temperature as much as it is geometry. If the manufactured part is flat, and we paint only on one side, a part that printed wonderfully can warp as the paint dries.
External Factors
Heat and humidity are the biggest external factors that cause warping in a 3D printed part. These can be from a range of sources, including storing the piece in a hot facility or shipping it in a hot vehicle.
The manufacturing facility´s climate can affect some 3D printing processes and parts. High humidity coupled with heat can cause a part to warp if it´s not stored in a temperature- and humidity-controlled environment. The material chosen contributes to this as well. In our French facility, for example, we use a composite, high-temperature material (called HST) exclusively for SLS, as it´s easier to build a flat box with HST versus other materials. The presence of glass fibers in this material limits the shrinkage along the X-axis of the part (parallel to the machine´s roller movement) and, thus, helps to reduce the risk of distortion. In addition, the HST material is designed to handle higher temperatures.
Our southern U.S. team tries not to ship SLS-printed parts on Fridays, particularly during the hot summer months. If the parts are a warp risk, they´re also packed in insulated boxes, but that solution only lasts for 24 hours, which won´t carry a part or prototype through a weekend. Customers can also have parts shipped to their homes or another location if they need the part quickly and know it won´t arrive until the weekend.
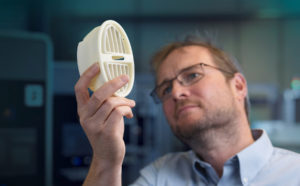
What else can you do?
Talk to us! Our experts can help make sure your part does not warp if your application needs precision or strength. They can also recommend different materials or processes that will achieve better results for your purpose.
If you´re trying to mitigate costs or on a strict deadline, tell our team those considerations, too. It can sometimes be more costly (in both time and money) to reprint a part than it is to print with another material or different process.
It all boils down to how you intend to use the part. SLS uses a more durable material, and the longevity of the part is better. SLA can print flat parts more precisely, but the material won´t hold up like SLS materials will.
Also, if your application will work with a minor warp in one area but needs another area to be perfectly flat, we may be able to give one aspect priority and sacrifice another aspect if you´re unable to shift processes or materials. We always work with your goals in mind and strive to print with your initial choice of process and material.
Bottom Line
3D printing is not an exact science, and there are no specific rules for these materials. Warping is linked to the technology itself. While we do everything in our power to ensure the part does not warp, we cannot always tell what will happen until it´s printed. Sometimes there is no choice other than to print the part or prototype and see what happens. Even with our extensive experience, we can´t necessarily predict the outcome just by looking at a drawing. However, we will always strive to make sure our we meet our customers´ goals and expectations.
We know deadlines are tight, and you need accurate parts in hand as quickly as possible. Our internal processes help ensure customers don´t lose time to rebuilds or issues (like warping) that could be avoided.
If you’re looking for an experienced partner in additive manufacturing and 3D printing, check out our additive manufacturing capabilities today.
We’re here to help keep your projects moving forward – begin a quote now or contact an expert.