Quickparts offers both urethane casting and low-volume injection molding services for those who need a low volume of relatively complex parts. These are very different processes, so understanding the pros and cons of both will help you determine which process is right for your needs.
Low Volume Injection Molding Services
Our low-volume injection molding service gives you the option of Quick Molded Parts or Prototyping/ Bridge to Production Molding.
Our Quick Molded Parts tooling is made from aluminum. Due to the soft nature of the metal, tooling can be completed very quickly, and parts can be made in as few as 5 days., Quick Molded Parts are, however, restricted in terms of quantity, size, and geometry of the part. The mold typically retains its integrity for 250 parts, and achieving a smooth, shiny surface finish may require secondary processing. The size cannot exceed 80mm x 80mm x 50mm (3in x 3in x 2in). Additionally, the part cannot have sharp angles or features like undercuts or protrusions that require sliders or lifters. Quick Molded Parts can give you the parts you need fast but not all materials can be used. The materials that can be used are limited to 15 engineering plastics. However, for parts that fall within the limitations, this is an economical option to get a low volume of high-quality injection molded parts.
Prototype molding uses a proprietary insert and steel base system. The customer invests in the insert, which has a lifetime of at least 2,500 shots (guaranteed) and up to 10,000 shots. The single-cavity inserts are made from high-grade aluminum. Parts can be made using a wider range of production materials, and more complex parts requiring sliders can be made. However, the tooling has to be designed and made which takes about 5 days before manufacturing can begin. This is an excellent option for those who need more parts than quick mold or have a more complex geometry.
Urethane Casting
Urethane casting, also called vacuum casting, is typically used for prototyping and very low-volume production runs. Parts can be end-use and resemble injection molded parts with regard to surface finish, color, and material properties. The parts are molded in a low-cost silicone mold, which costs a mere fraction of a steel tool. The molds are made by 3D printing a master pattern, usually in SLA or SLA materials, which enables fine detailing and including texturing. Silicone is poured over the master model and allowed to cure, creating the silicone mold. The master model can be used between 25 to 30 times before obvious degradation occurs. The tool and the part can be ready in 4 days. Aside from tool life, there are two further drawbacks to urethane casting: first, while there is a wide range of materials that can be used, from rigid polyurethanes to flexible rubbers, these are injection molding simulants and may not display the same properties as injection molding plastics when it comes to tensile strength, durability, and chemical resistance. Second, all cast urethane materials have low heat resistance, typically under 200˚C, although there are some with flammability ratings that enable use in certain environments.
The thermoset polyurethanes used in urethane casting can be pigmented or transparent, providing aesthetic flexibility without considerable post processing.
For Low Volume Injection Molded Services or Urethane Casting, Trust Quickparts
When choosing between low-volume injection molding and urethane casting, it’s essential to consider the specific requirements of your project. Quickparts has a variety of options, allowing you to select the process that best meets your needs in terms of speed, material choice, and complexity. Whether you require a quick turnaround for simple parts or a more detailed, flexible solution, Quickparts has the expertise and technology to deliver high-quality results. Contact us to learn more about how we can support your low-volume production needs.
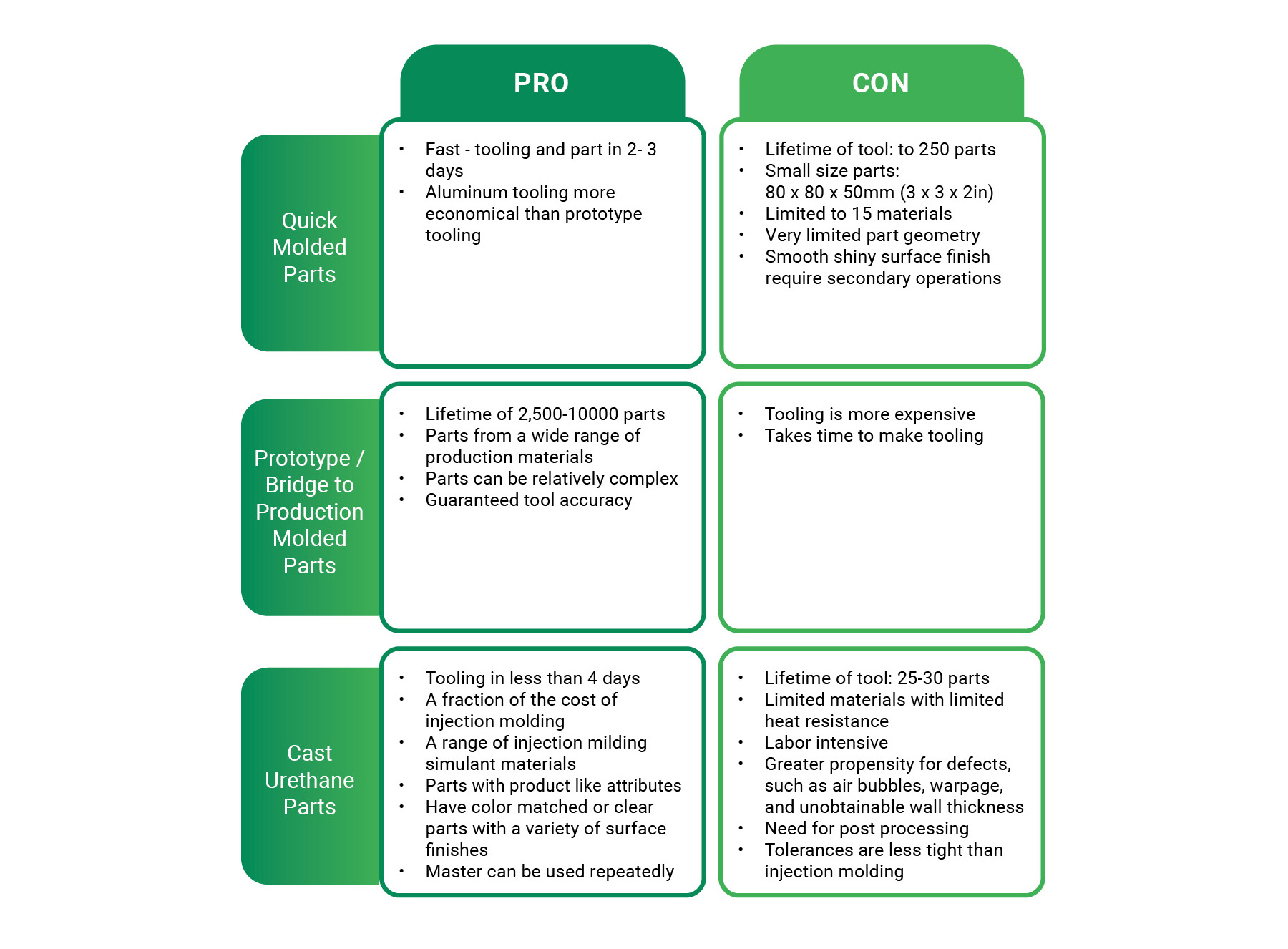