The risks related to thin walls and fragile features are common in additive manufacturing. Known as “knife edges,” these are very thin areas in 3D design files that are below printer tolerances for integrity and stability in the piece. These areas can cause issues, such as deformities, making part of the piece fragile, or destroy the integrity of the part altogether if the knife edge is not rectified.
However, knife edges are not always “bad.” Sometimes, they’re unavoidable, such as when a part needs to be ultra-thin to work properly or look like it should. Other times, the designed area creating a “knife edge” can cause a ripple or other issues in a piece that might interfere with its usefulness. And in certain instances, knife edges are intentional.
So how do you know when knife edges are unavoidable versus when they can be mitigated (and how to do so)?
You pick the right partner with the right equipment and the right experience.
Working with Us
When working with Quickparts, you don’t have to worry about whether the file will produce the best possible result – we ensure this by reviewing your design files to catch potential issues before we begin to print your project.
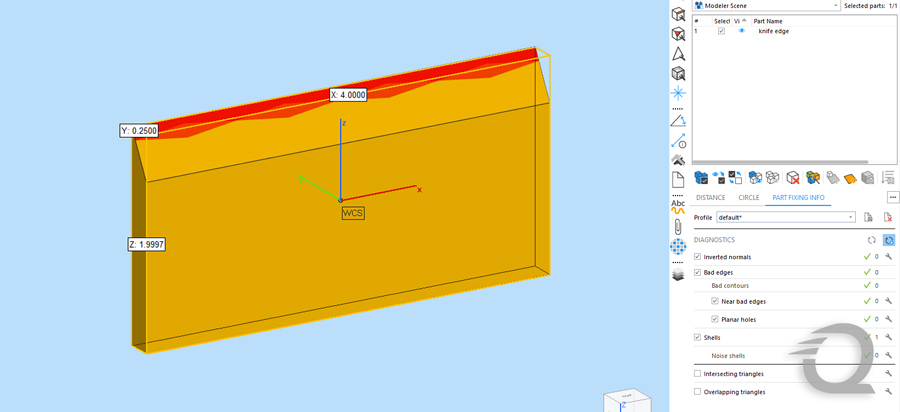
At the start of every project, each customer uploads their design files before obtaining a quote. Files instantly upload to a proprietary system that checks the file integrity and ensures it’s ready to go. For certain 3D printing processes, like DLP, SLA, and SLS, Quickparts customers can get an instant quote from just a request and file upload to start a new project. For these projects, the process is seamless and fast, and project turnaround time can be a matter of just a few days. For more complex projects, design files need a manual review, but we work to ensure it’s completed quickly, and the process is just as easy!
Setting Up for Success
Each manufacturing process requires a different minimum thickness for the part to print successfully and without a knife edge. If the design file does not meet those minimum thicknesses, the end result can be warping or a rippled edge.
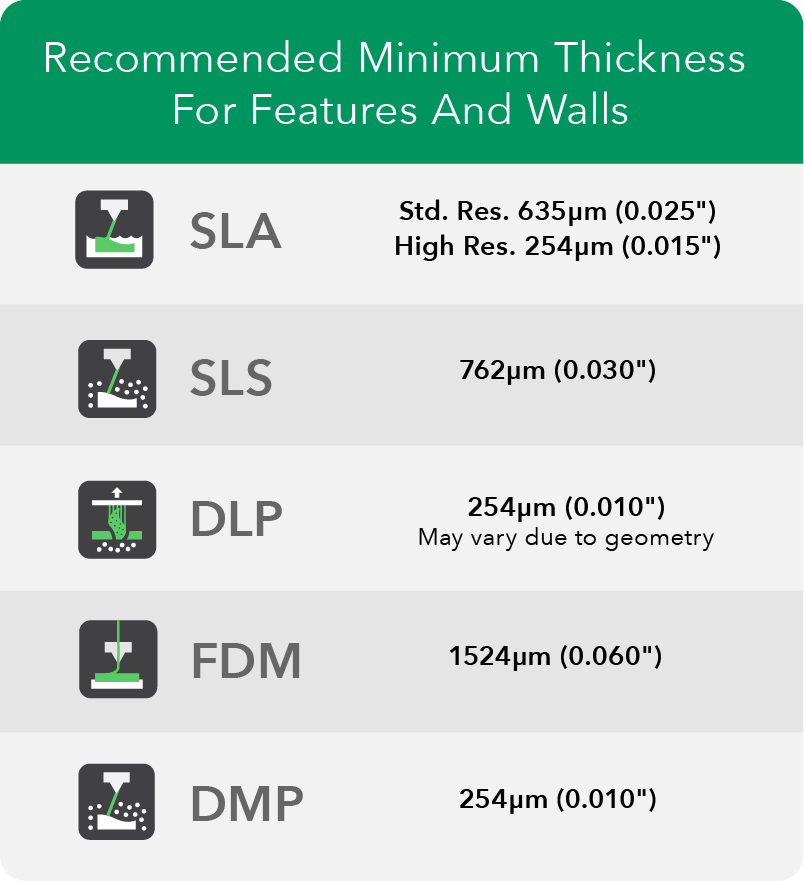
*An entire part measuring 0.015” or 0.025” for standard resolution may not make it through the post processing due to how thin – based on geometry of the part.
Our first order of business is to understand what the part will be used for and whether the knife edge is necessary or can be mitigated somehow. Some ways to do so are by building up the edge in question, running the piece with a different process, or changing/editing the file.
If the customer chooses to proceed even though the edge could be different than they envisioned, great! The project moves to the next step.
If the customer does not want to proceed with the knife edge, our team works with them to better understand the project overall and how this part fits within it. In some cases, our Quickparts experts can recommend a different process to achieve the desired result for that project. In other cases, the customer notes that they understand the risks and have decided to move forward with printing as is.
Once the file is set up for success and the team ensures the product will meet the customer’s requirements, it’s time to print!
About Quickparts
Quickparts has been at the forefront of the additive manufacturing industry for decades. The company delivers the broadest range of additive manufacturing technologies and materials in the industry.
We know deadlines are tight, and our customers need accurate parts in hand as quickly as possible. Our internal processes help ensure customers don’t lose time to rebuilds or issues (like knife edges) that could be avoided. If you’re looking for a partner in additive manufacturing, check out our additive manufacturing capabilities today.
We’re here to help keep your projects moving forward – begin a quote now or contact to an expert.