Die Casting
When looking for fast large-scale production of parts without sacrificing detail and surface quality, die casting is a perfect manufacturing option.
But you won’t get the full benefits of die casting without knowledgable engineers, a communicative project managing team, or industry leading facilities.
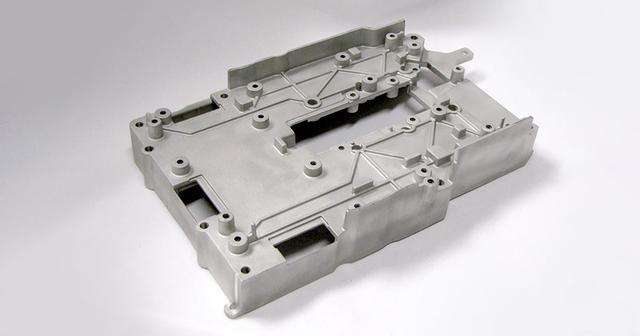

Quickparts takes care of your project with our integrated manufacturing capabilities, allowing us to rapidly produce any part and take your project from prototype to production quickly and efficiently.
How it Works
Die casting describes the process of forcing molten metals under high pressure into machined mold cavities to produce metal parts. The die casting method is especially suited for applications where large quantities of small- to medium-sized parts are needed with good detail, fine surface quality and dimensional consistency.
Using Quickparts for your die casting service comes with the backing of an industry innovator and leader for both additive and manufacturing services. Our team of expert engineers and our global network of facilities gets your parts to you quickly and efficiently, no matter where you need them.
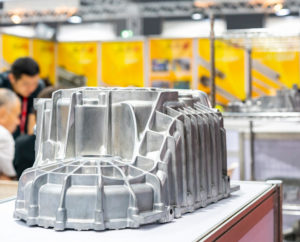
Let us be your resource to determine which manufacturing process is right for your project.
About Quickparts
Quickparts is a pioneer in the 3D printing world.
We are the originator of a full digital manufacturing platform that delivers on-demand additive and traditional manufacturing services. From rapid prototyping to appearance models and volume production, Quickparts operates the most advanced technology and possesses the expertise to handle any additive manufacturing project.
With facilities stationed around the world, each staffed with experienced engineers laser-focused on meeting your specific requirements as effectively and quickly as possible, you can trust Quickparts with all of your manufacturing needs.
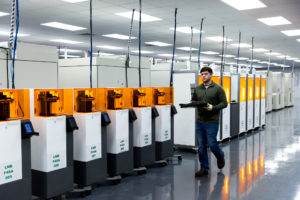
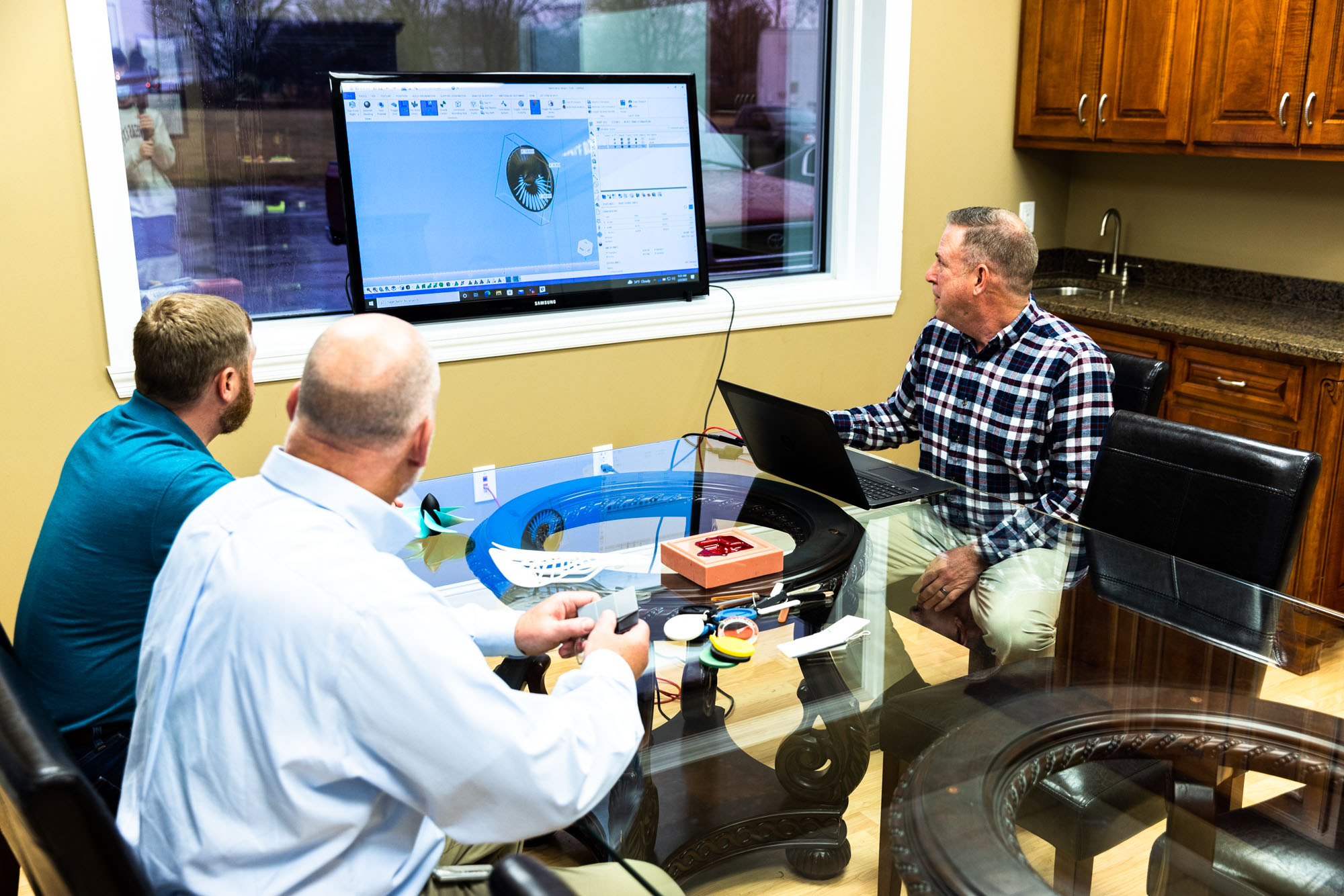
Get Started
You’re seconds away from starting your Quickparts project.
Die Casting Services- Get Premium-Quality Engineered Products
Why would you choose die-casting for your project?
This production process ensures high accuracy, reliability, and versatility.
We also prefer die-casting for metal part production because it eliminates the need for making secondary operations. However, our die-casting parts can also be post-processed in the desired finish based on the CNC machined counterparts.
Should you choose the die-casting method for your products?
Die-casting is the best option if you need to design non-ferrous metal products within the shortest time. As this process uses reusable molds, we ensure high-speed production. This process has the versatility to develop products of various sizes or shapes. Our die-casting professionals can take advantage of the automated process. So, you can invest in our services to design industrial, commercial, and consumer products with medium-sized parts.
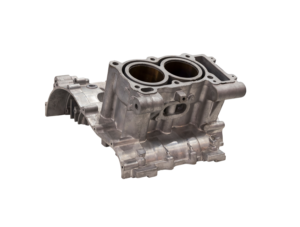
Our die-casting process
Die casting involves mold tool (die) fabrication, and the die may have more than one cavity. The process is effective for soft alloys like zinc and aluminum alloys because of low melting temperatures.
We inject molten metal into the cavity so that it can take the desired shape. Then, when we remove the part, it gets hardened.
We use low to high pressure based on the scope of your die-casting project. This is because it repeatedly produces complicated, tight-tolerance parts at a considerable production volume. However, we also apply semi-solid casting and squeeze casting methods, which are more innovative than other conventional processes.
Die casting solutions- Hot chamber and cold chamber
At Quickparts, we specialize in both types of die casting- Hot chamber and cold chamber.
We choose lead, magnesium, and zinc for hot chamber casting methods. We fill the holding pot with metal and heat it with the hot chamber casting. Pressure helps in holding the meal together. When the metal is cool, the die opens. You will then receive the casted piece.
On the contrary, we can conduct the cold chamber casting at room temperature. There is a direct connection between the mold and the shot chamber. We choose aluminum for this die-casting process.