Injection Molding Tooling and Parts for Low Volumes
Accelerate your product development cycle with Quickparts’ advanced injection molding solutions. We provide steel and aluminum tooling to create high-fidelity prototypes and pre-production parts manufactured in production-grade materials. This allows for rigorous testing of functionality, durability, and reliability – all before committing to full-scale manufacturing.
- Production-Grade Materials: Prototype and bridge parts made from the same materials used in final production runs, ensuring accurate performance testing.
- Injection Molding Design Freedom: We handle most geometries with ease, and incorporate overmolding, insert molding and component integration, so you can bring your innovative ideas to life without limitations.
- Validate Your Design: Test functionality, durability, reliability, and conduct crash tests with confidence using real production-grade parts.
- Bridge the Gap to Production: Seamlessly transition from prototyping to full-scale production with our bridge-to-production solutions.
Tooling and Parts
Our steel and aluminum tools are CNC machined on-site to standard tolerances of ±0.1mm. For parts requiring tighter tolerances, such as for medical devices or aerospace parts, tolerances to ±0.025mm are achievable.
Tool life is to 2,500 parts, and Quickparts ensures your mold inserts meet the highest quality standards. You retain ownership of the mold inserts used for prototyping or bridge production.
Maximum build size: 200 x 200 x 114mm or 8″ x 8″ x 4.5″.
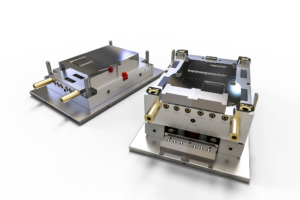
Over 30 Materials in Stock
We offer a wide range of materials to match your specific requirements. You can also provide your own material.
Tool Ownership:
In accordance with Ts & Cs. In most instances, the customer will own the mold insert and tool storage is offered for 24 months.
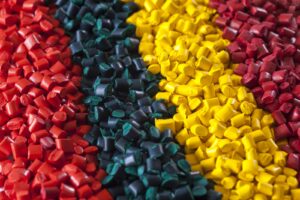
Fast Lead Times:
2 – 3 Days for Production Agreements, including DfM: Our team will promptly review your project and provide expert recommendations. Production usually commences 2 – 3 days after PEG.
2 to 5 Weeks for T1 Samples After Customer Approval: Get your prototype or bridge parts quickly with our efficient production process.
Technical Specifications
Maximum Part Size |
Tolerances |
Wall Thickness |
Radii |
200 x 200 x 114mm or 8″ x 8″ x 4.5″ | DIN EN ISO 20457 class T6 (W); further tolerances according to customers’ 2D drawing | Material dependent, typically minimum 0.8 mm/0.03″ | Can do EDM – sharp corners, according to customers’ specifications |
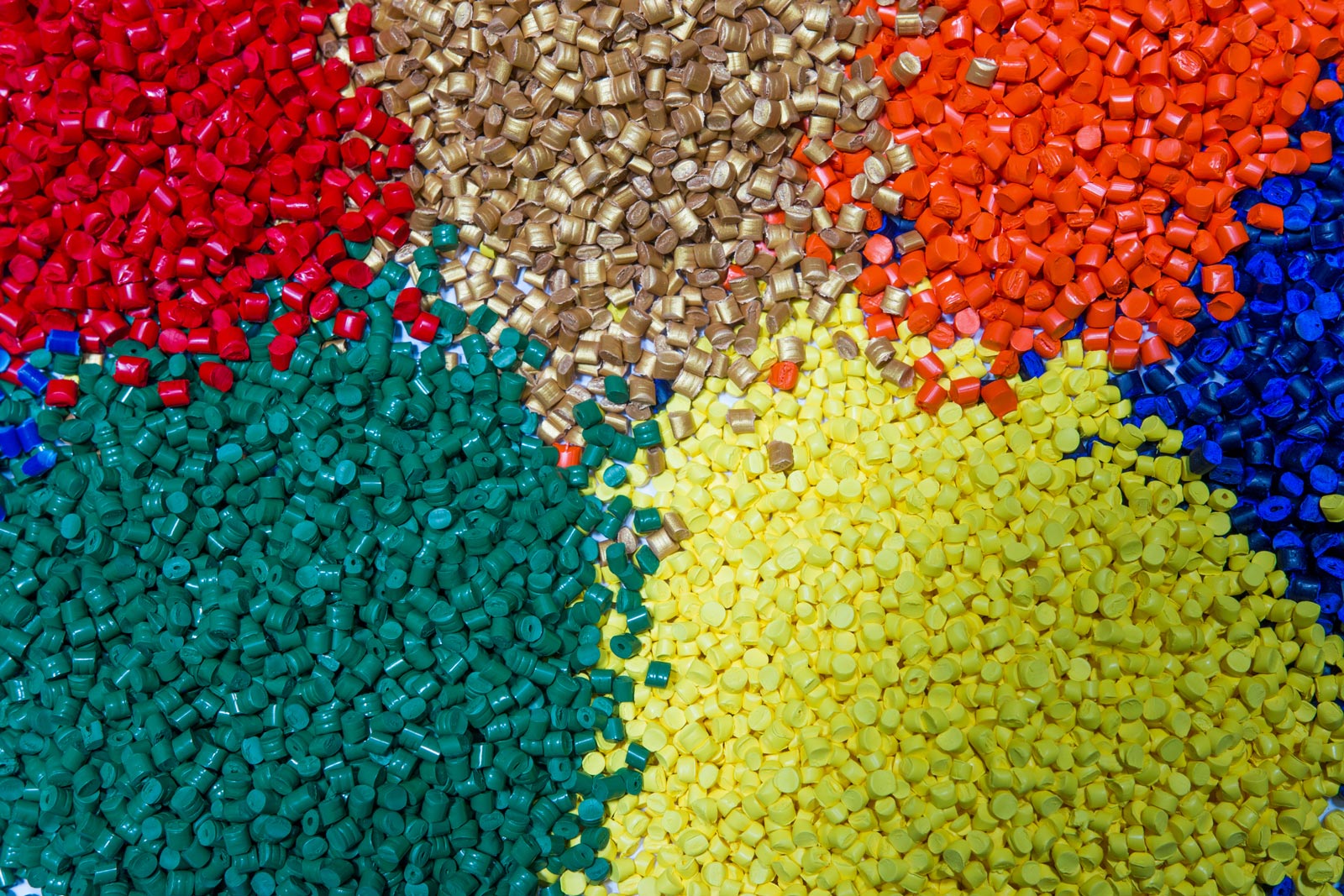
Ready to order?
Upload your CAD files or contact us today for a free quote and to discuss your prototyping or bridge-to-manufacturing needs.
ABOUT QUICKPARTS: One of the World’s Leading Injection Molding Suppliers
We are the originator of a full digital manufacturing platform that delivers on-demand manufacturing services. From prototyping to high volume production, Quickparts operates the most advanced technology and possesses the expertise to handle most manufacturing projects.
With facilities stationed around the world, including two centers of Injection Molding excellence, each staffed with experienced engineers laser-focused on meeting your specific requirements as effectively and quickly as possible, you can trust Quickparts as one of the premier suppliers with all of your manufacturing needs.
We have a streamlined approach to mold making, plastic Injection moulding, and engineering processes. We have a separate team of quality control specialists who understand the importance of value, quality, and consistency in moulded products. This is how we differentiate ourselves from our competitors.