5 Tips on Getting the Best Result with Your File
When designing a part for CNC machining, it is beneficial to think about the manufacturing process. Consider things like materials, tooling needed, setup time, tolerances, finishes, etc. You can use these considerations to make smart decisions for your design, including designing the components to improve pricing and lead time.
Here are some considerations:
- Sharp internal corners are one of the easiest areas to spot design-for-manufacturing errors. Internal corners should have radii, as the tools that machine those features are round, and, therefore, design files need to denote a radius. It is a common practice when designing for machined components to include a radius that is equivalent to the depth of the pocket divided by 8 or greater. This will help ensure that standard tooling can be used for the machining process. For example, if the pocket is 1″ (25.4 mm) deep, the radii for internal corners would need to be 0.125″ (3.175 mm) or larger. This will allow for a standard ¼” (6.35 mm) endmill. When designing radii and internal corners, larger is always better.
- Drilled holes are occasionally a source of heartache. Here are a few rules to help you avoid potential pitfalls with your design.
- Keep the depth-to-diameter ratio smaller than 8. If you have a hole that is ½” (12.7 mm) in diameter, do not go any deeper than 4″ (101.6 mm). However, some tooling (drills) will easily go beyond this suggestion, but even with special drills, the likelihood of maintaining tighter tolerances begins to dissipate.
- Keep holes away from the edge when possible. Holes near an edge tend to push material out, causing a bubbled effect.
- Blind holes (holes that do not go all the way through the material) that are drilled will have a drill point at the bottom. Therefore, it may be necessary to increase the depth by 25% to compensate for this point, particularly if it will be a tapped hole later.
- Design for standard drill sizes. Although custom drills can be made, it is costly and time-consuming.
- Be careful with wall design.
- Avoid thin walls entirely. Thin walls decrease the integrity of the component and cause undue stress. Too-thin walls also make holding tolerances very difficult and impair our ability to create an aesthetically pleasing part. Try to keep the wall thickness at greater than 0.030″ (0.762 mm); wall thickness should increase as it gets taller.
b. Avoid drafts on walls. Any time that you can eliminate a draft feature on a wall, boss, cavity, pocket, or ledge, it is good to do so. This will eliminate the extra steps needed in the machining process to align with that particular planar surface.
- Avoid thin walls entirely. Thin walls decrease the integrity of the component and cause undue stress. Too-thin walls also make holding tolerances very difficult and impair our ability to create an aesthetically pleasing part. Try to keep the wall thickness at greater than 0.030″ (0.762 mm); wall thickness should increase as it gets taller.
- Choose the “right” material.
- Harder materials are more difficult to machine and take longer. Materials like stainless steel are exponentially more time-consuming than a material like aluminum. If you do not need the harder material’s properties, choose a material that is easier to machine.
- Non-standard materials can also be more difficult to source and will add to the lead time and cost.
- Consider part size with regard to material. If a material is only available in a 4″ × 4″ (101.6 × 101.6 mm) cube, it may not be the right material for a 0.5″ × 0.5″ (12.7 × 12.7 mm) component. Likewise, if the part is large, you should choose a material that will be available in a larger stock size.
- Don’t over-tolerance your component. Unnecessarily over-tightening your tolerances can greatly increase the time and cost associated with creating your component. When deciding tolerances, consider what would be the loosest tolerance you can accept for the form, fit, and function of your project. Some materials are inherently difficult to maintain tight tolerances for any number of reasons. This should also be considered when designing for machined components. For example, if you need a plastic part with tighter tolerances, we recommend selecting PEEK versus Delrin because of its stability and structural integrity.
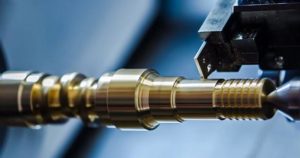
As you can see, there are many considerations when designing for manufacturing with CNC machining. If you are designing a part for CNC machining and have questions about your project, contact our experts today.
Check out our manufacturing capabilities if you’re looking for an experienced partner who can help with your CNC machining needs. If you have a design file and are ready to start, begin a quote now.