CNC machining is a traditional manufacturing process in which computer-run programs control how machines manufacture a component. Using specialized software, CNC programs can control everything from the motions the machine makes to the spindle speed, turn coolant on or off, and much more.
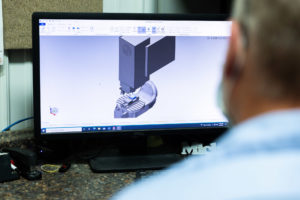
CNC is an acronym that stands for Computer Numerical Control, which comes from the older term, Numerical Control (NC), and refers to controlling machine tools via computer. The computer tells the machine things like how fast to turn the spindle, how fast to move the cutter, which directions to move, how much to move in one direction, coolant on or off, change the tool, and more. The languages used to program CNC machines are called “G-code,” specialized computer code created via CAM (computer-aided manufacturing) software to help make coding for CNC machines easier.
Customers choose CNC machining as the preferred manufacturing process when they need highly precise or high-quality parts or when the materials are particularly difficult to work. There are many kinds of CNC machines, including vertical mills, horizontal mills, lathes, live tooling lathes, lasers, water jets, EDMs (electrical discharge machining), routers, plasma cutters, and more.
History of CNC
Before CNC machines, machining tools were controlled manually by machinists. With a manual machine, the machinist operates the machine by turning handwheels. With CNC, a computer controls servos that operate the machine. Essentially, they are machining robots. NC, and later CNC, allowed for tremendous increases in productivity for machine tools because the machinery could be run automatically without requiring constant attention from their operators.
The first commercial NC machines were built in the 1950s and ran from punched tape. While the concept immediately proved it could save costs, it was different from the norm and was slow to gain ground with manufacturers.
To promote adoption, the US Army bought 120 NC machines and loaned them to various manufacturers so they could become more familiar with the idea of numerical control. By the end of the ‘50s, NC was catching on but still had some issues. For example, there was no universal language, so each manufacturer pushed its own language for defining numerical control or part programs.
Several key developments brought CNC along quickly during the 1960s:
- Standard G-Code Language for Part Programs: G-code originally dates to MIT around 1958 and was used in the MIT Servomechanisms Laboratory. The Electronic Industry Alliance standardized G-code in the early 1960s.
- CAD came into its own and rapidly replaced paper drawings during the ‘60s. By 1970, CAD was a decently sized industry.
- Minicomputers, like the DEC PDP-8s, became available in the ‘60s and made CNC machines cheaper and more powerful.
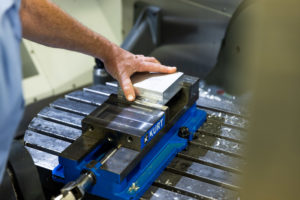
By 1970, the economies of most Western countries had slowed, and employment costs were rising. With the ‘60s having provided the necessary technology foundation, CNC took off and began steadily displacing older technologies, like hydraulic tracers and manual machining.
U.S. companies had largely launched the CNC revolution, but they had been overly focused on the high end. Germany was the first to reduce prices for CNC, and by 1979, the Germans were selling more CNC than the U.S. The Japanese repeated the same formula even more successfully and took the lead only one year later. In 1971, the 10 largest CNC companies were all U.S. companies, but by 1987, only one was left, and they didn’t make the top 5.
More recently, microprocessor technology has made CNC controls even more cost-effective, resulting in greater availability for hobby and personal markets.
Affordable CNC machinery also paved the way for CNC use in prototyping, along with 3D printing. Earlier, CNC was confined primarily to production shops.
Common Materials for CNC Machining
-
STAINLESS STEEL
Stainless steel is a versatile raw material for precision machining and preferred in a variety of applications for its strength and corrosion resistance. There are many different types of stainless with various treatment options that change its material properties and the way it machines. The alloy/grade determine price, availability, and machinability. -
ALUMINUM
Aluminum has many advantages, including light weight, easy to machine, non-magnetic, corrosion-resistant, and inexpensive. Advances in cleaning and machining make aluminum a more useful material than steel in some cases. For best results, aluminum welding must be handled by an experienced machining shop. It can be machined to tight tolerances and can be plated with many different materials to make it harder or more conductive as a cheaper alternative to steel, stainless steel, or copper. - BRASS
Brass is another cost-effective material. Its advantages include ease of machining; a smooth, clean finish; non-sparking; holds tolerances; and threads well. Brass is good for intricate parts that require sophisticated features but should not be used in certain applications because of zinc and tin in the material. One of its most common uses is cast parts. -
TITANIUM
Highly prized and useful for machining, titanium resists both heat and corrosion and has the most significant strength-to-weight ratio of any metal. It is also lighter (in weight), inert, and biocompatible, making it ideal for a wide range of applications, from aerospace to medical. However, titanium can be difficult to machine and costly. If you need machined titanium parts, choose an experienced precision machining shop, like Quickparts. -
STEEL
Valued for its strength and durability, steel is one of the most popular metals for all types of manufacturing. Like stainless, steel is based on the grade, and each grade has a specific purpose. Steel is easy to weld compared to other common materials, and typical uses include industrial, automotive, and oil and gas. -
COPPER
Copper is another metal highly prized for precision machining. Copper provides the benefits of versatility, durability, electrical conductivity, and natural corrosion resistance. Copper doesn’t hold tolerances as well as aluminum however it is a much better electrical conductor especially when plated. -
BASIC PLASTICS
Inexpensive and known for use in injection molding, plastic can also be used as an inexpensive, non-metal, non-conductive raw material for machining. Plastic machined parts are inert and adaptable for a range of different properties, making this material useful to a variety of industries, including industrial, electronics, scientific, and more. -
ENGINEERED PLASTICS
Plastic materials that have better mechanical and/or thermal properties than more widely used commodity plastics are called “engineered plastics” and have been designed with the strengths of its metal counterparts. In semiconductor applications, for instance, engineered plastics replace quartz and aluminum; it is also more common in medical instruments because it can be cleaned easily.
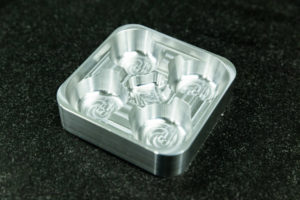
How Can Quickparts Help?
CNC machining uses a wide range of materials, allowing us to manufacture parts that will suit many applications — begin a quote now. To learn more about CNC machining or how Quickparts can help with the parts and components you need, reach out to one of our in-house experts today.